Diverse functions maximize the motor performance, making the motors quieter, faster and easier to use
CKD NIKKI DENSO’s servo drivers have each servo control loop optimized, enabling fast positioning and high stop stability for direct drive motors and linear servo motors. Moreover, a rich set of gain tuning parameters lets you tune the gain as appropriate for various load shapes. In addition to the existing VPH Series, the lineup includes the VPV Series that features new functions. Also, an intuitive system support tool is available that streamlines the startup process.
Support of industrial networks
- EtherCAT (VPH and VPV (planned))
- SSCNETⅢ/H(VPH)
- MECHATROLINK-Ⅲ(VPH)
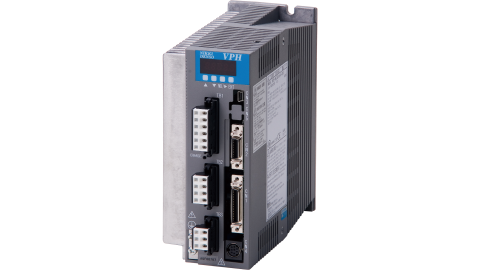
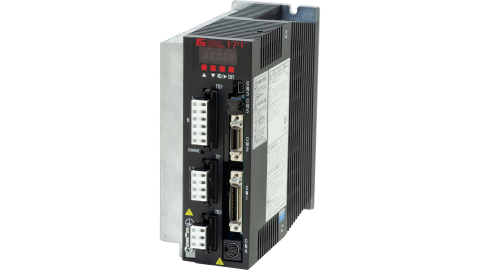
Performance and functionality specifically intended to control DD motors and linear servo motors
Superb speed stability
Significant suppression of torque ripples
Suppression of torque ripples further enhances the speed stability.
Easy tuning even under a large inertia load
Feedback filter auto setting function
At the time of auto-tuning, a feedback filter appropriate for the load is automatically set, suppressing the speed detection ripples and ensuring easy tuning even under a large inertia load. Smooth operation can easily be achieved.
Improvement in stop stability
Stop-time filter function
Improvement in stop-time torque accuracy
Stop-time vibration is suppressed even under a large inertia load.
Enhancement in the low speed gain switching function
As the conditions switching from normal to low speed gain, it is possible to set not only speed but also other factors such as deviation and whether a command is issued or not.
Smooth operation reduces the positioning time
2-stage S-curve acceleration/deceleration control function
Torque waveforms are controlled with quadric curve, substantially reducing the impact during acceleration/deceleration. This prevents vibration even if the acceleration/deceleration time is shortened, thus reducing the positioning time.
Improvement in safety in case of collision
Collision stop function (VPH (option) and VPV)
The servo driver detects a collision between the load connected to the motor and some other mechanism and brings the motor to a quick stop, thus reducing unintended mechanical interference and damage to the mechanical system due to the collision.
Visualization of alarms
History of 25 alarms and electrification time display (VPV)
- The history of 25 alarms is stored. What’s more, the alarm occurrence time (relative to the servo driver operation time) can be displayed.
- The history is recorded even if the same alarm occurs in succession.
- The chronological history of alarms that have occurred is displayed, which is helpful in troubleshooting.
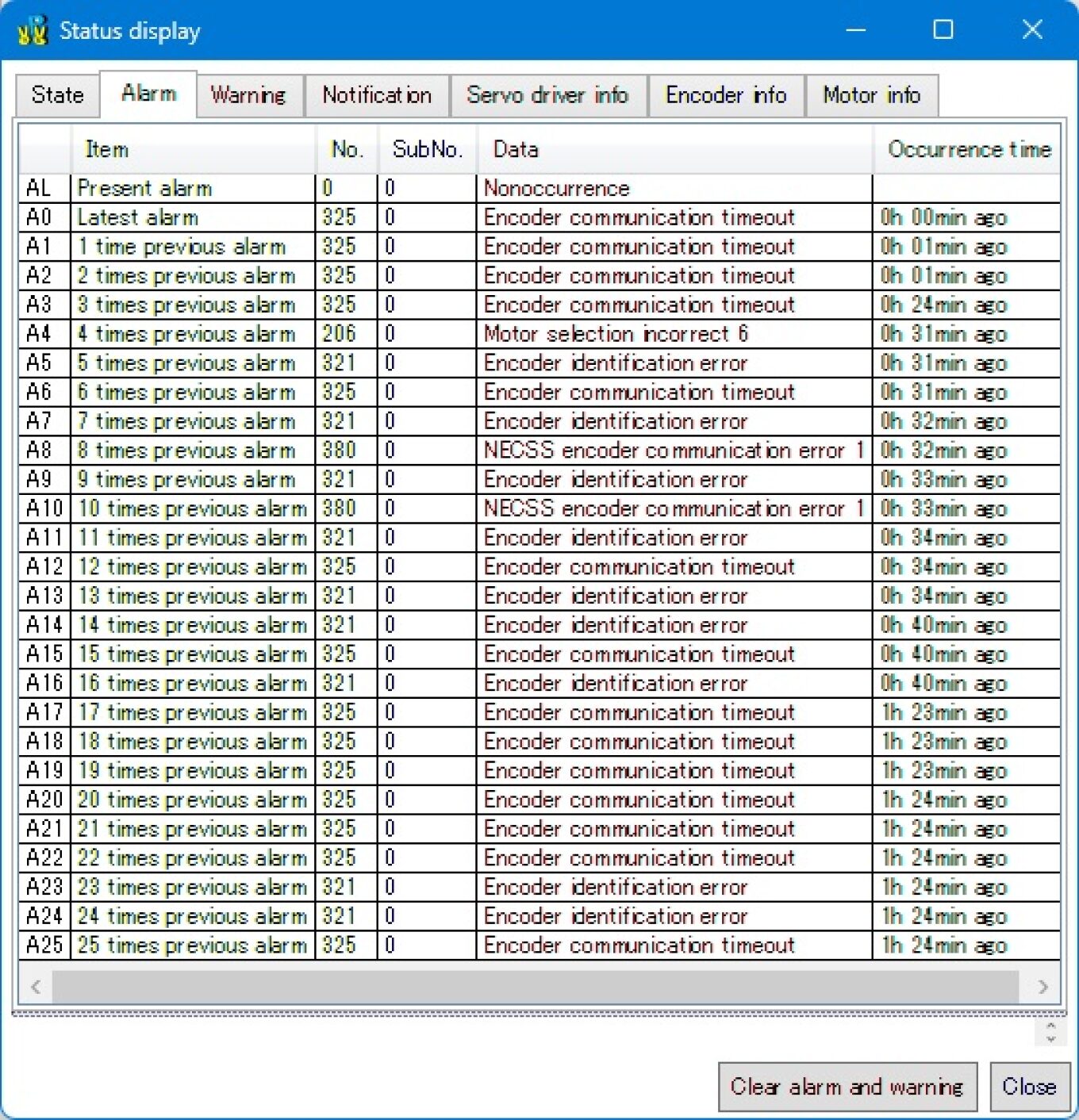
Consumable replacement notification
Notification function (preventive maintenance) (VPV)
- As a preventive maintenance function, a consumable replacement notification (based on the time of use) can be provided.
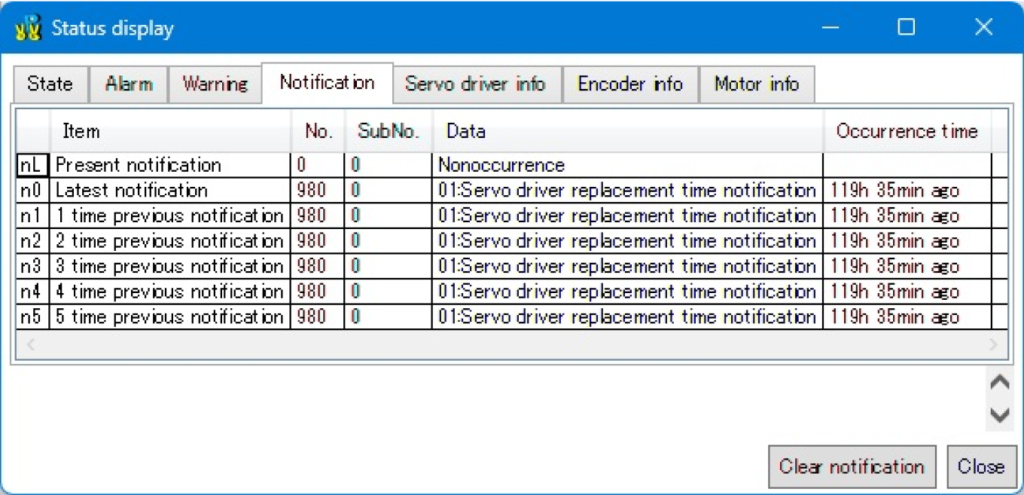
Intuitive, easy-to-use system support tool
A rich set of adjustment, monitoring, operation, analysis, and editing functions
- Mechanical system matching and startup work are streamlined.
Automatic servo gain adjustment function (NiEAT)
- Interactive initial setup is supported for the major control method.
- Enter selection conditions to the direct drive motor selection calculation tool, and you can have the filter and gain value automatically adjusted until the selection conditions are met.
(Add the link to “Use cases of problems solved” for NiEAT.)
- Channel 4 of the oscilloscope function is used as an extended function, and I/O signals can be monitored at eight points simultaneously.
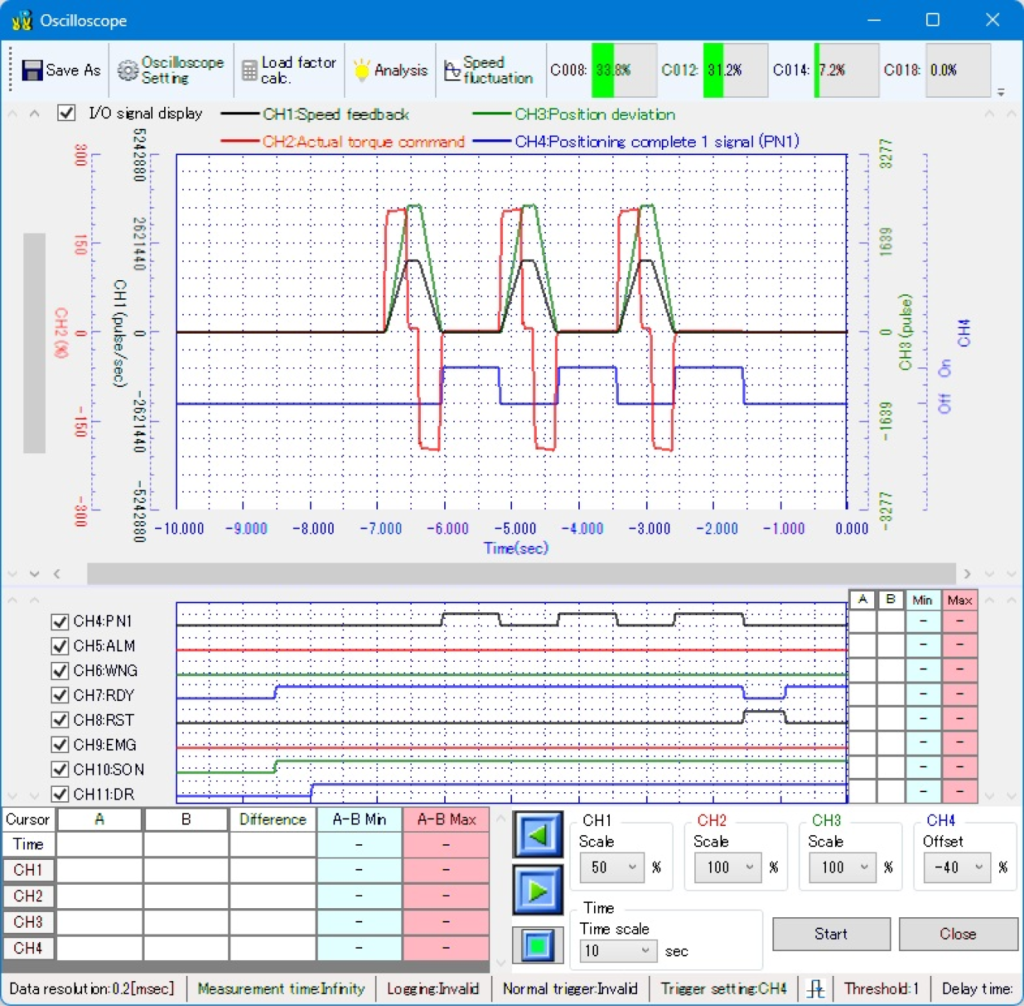
Operation evaluation function (VPV)
- The function lets you check the positioning in reciprocating or index motion, the positioning time for each position, the number of positioning complete failures, and torque.
- For example, you can analyze a 16-segment operation to identify a specific segment where the positioning time is slow.
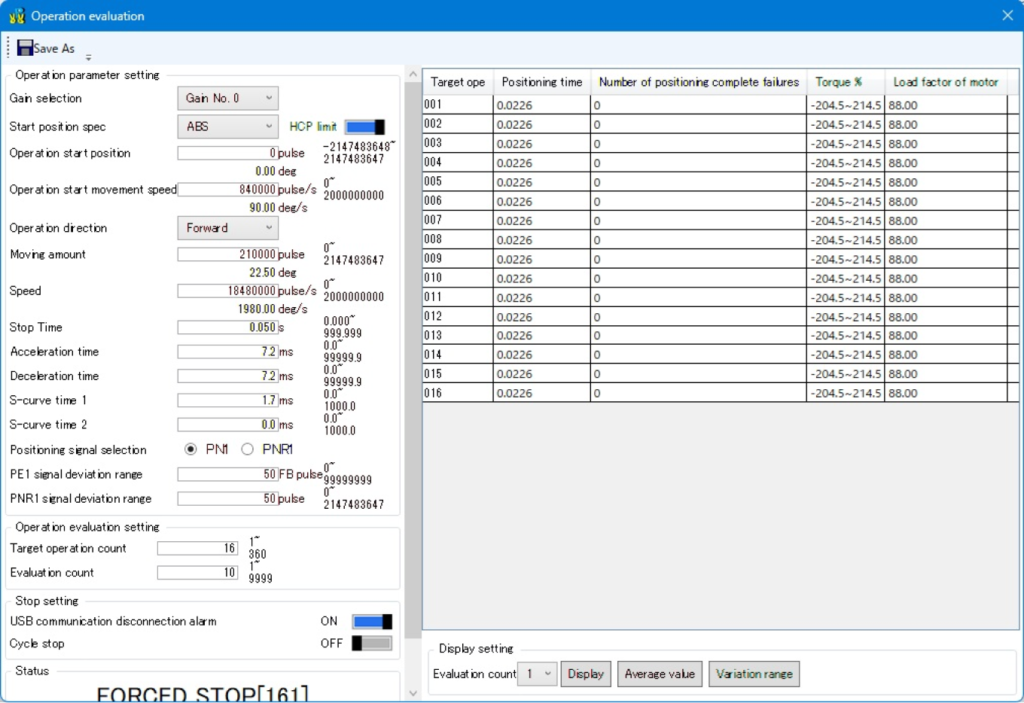