Direct drive motors have been introduced to the mechanical cam-based production line to turn it into an electronic cam-based one. The reduced takt time and greater flexibility in the operation angle have increased production efficiency.
The existing mechanism has limits in reducing the takt time and increasing production efficiency further.
We proposed introducing DD motors that directly rotates the mechanism and allows the operation angle to be changed freely. This improved the positioning accuracy and made the jig less prone to failure, leading to a substantial increase in production efficiency.
[Problem] The customer wanted to increase production efficiency by flexibly handling various workpieces in small quantities and enhancing the positioning accuracy.
In the case of mobile devices, for example, because every different model uses different types of parts, the existing mechanical cam-based production line requires changing the mechanism itself, making it difficult to handle various workpieces in small quantities. Moreover, since there is variation in positioning accuracy, the workpiece may get damaged when parts are fitted into it. There are also other factors that make the process very inefficient, such as the reduction in processing accuracy due to wear of the jigs and the cost of replacement. The customer wanted to increase the production efficiency of their equipment by enhancing accuracy.
[Proposal/solution] Increase the efficiency of the entire production process by introducing tilting DD motors with high positioning accuracy.
Electronic cam control synchronizes and interlocks multiple-axis servo motors. To reduce the operation takt time, high response is required on the motor side as well. The use of our direct drive motors brings the following benefits.
① The operation angle can be changed freely, easing the burden of machine setup even when handling various workpieces in small quantities.
② Positioning accuracy and repetitive accuracy increase significantly, alleviating the wear of jigs experienced before.
③ Our VPH Series servo driver can connect to the motion network specified by the customer.
④ The adoption of the high-response type τDISC HD-s Series improves the production takt time.
These benefits have successfully solved the problem. Since a major change was made to the equipment, it took time before a prototype was introduced. Now, the proposed solution has been introduced to some mass production lines, and the customer is discussing a plan with us to deploy it to another plant.
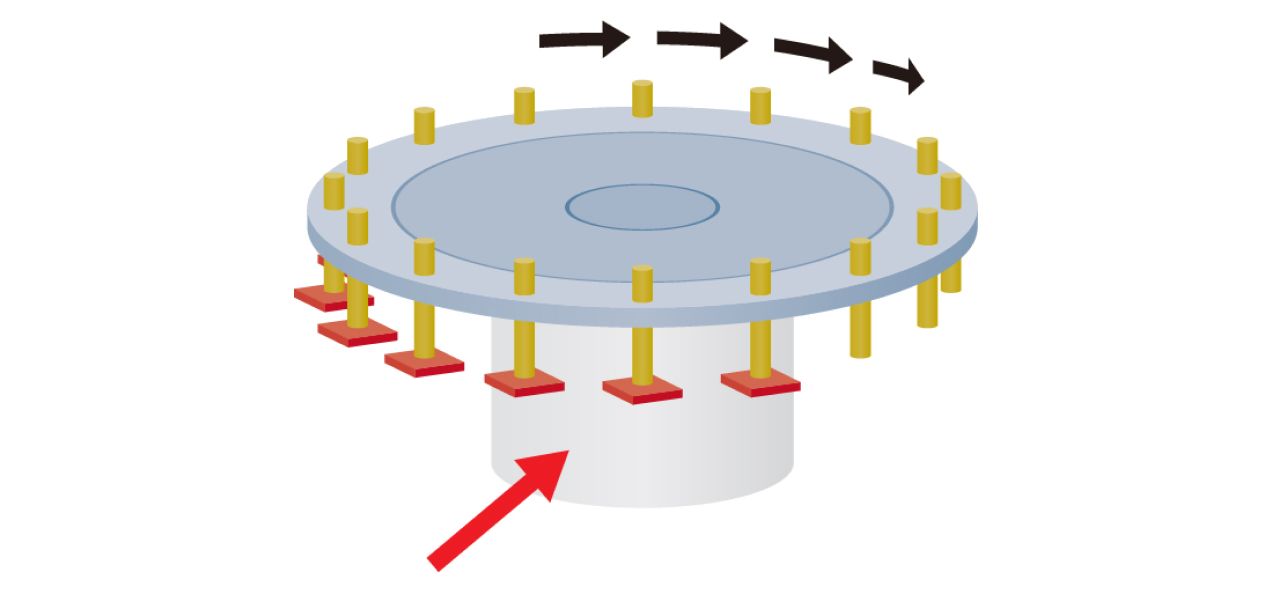
Key points in adopting our proposal
- High-response, high-accuracy positioning and reproducibility
- Motion network control using MECHATROLINK-III
- Customer-centered support
Related products
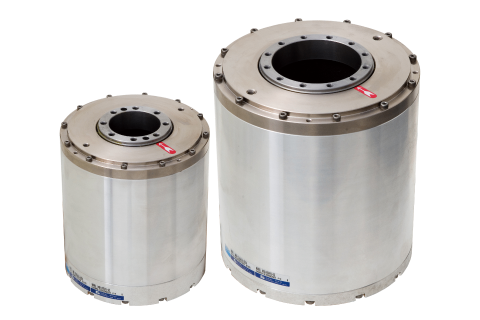
τDISC HD-s Series
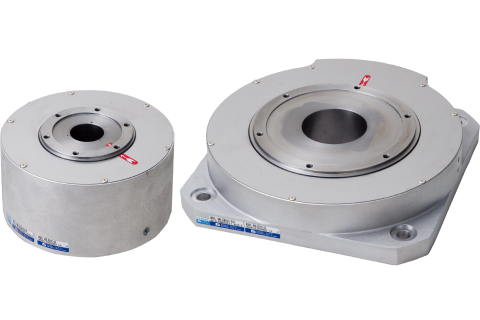
τDISC ND-s Series
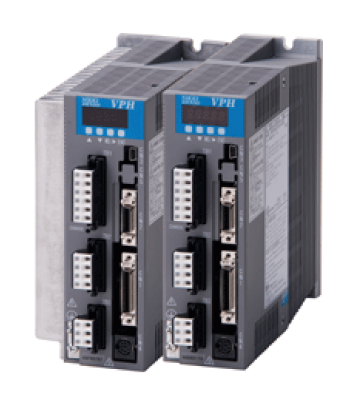
VPH Series