The vacuum deposition equipment of OLED displays had various problems, including speed stability during workpiece transport. The introduction of a vacuum linear servo motor solved these problems.
The vacuum deposition equipment had various problems, such as noise, waste, and maintenance, in addition to speed stability during workpiece transport using a rack and pinion mechanism.
Leveraging our know-how about vacuum, we introduced a vacuum linear servo motor, which reduced noise and improved operation stability, enabling even deposition.
[Problem] The customer wants to improve the various problems with the vacuum deposition equipment that occur during workpiece transport, such as speed unevenness and noise.
The organic solvent vacuum deposition equipment of OLED displays, which uses a rack and pinion for workpiece transport, has a problem in terms of moving speed stability. The rack and pinion mechanism has a simple structure and is easy to introduce due to its low price. On the other hand, it has various productivity problems, such as waste and noise generated from its engaging metal teeth and the stoppage of the equipment due to consequent frequent maintenance. The customer contacted NIKKI, a manufacturer abounding with know-how about vacuum, because they wanted to create equipment with a vacuum linear servo motor.
[Proposal/solution] Introduce a vacuum linear servo motor to reduce noise and improve operation stability.
Replacing the existing rack and pinion system with a vacuum linear servo motor reduced noise and improved operation stability. Introducing a vacuum linear servo motor requires special skills, such as designing a structure capable of withstanding the vacuum condition and selecting appropriate materials. The customer made a contract with us because they appreciated the quality of our product, including the know-how we had amassed, and our fined-tuned follow-up system. We took measures to specifically address the vacuum condition, such as introducing a water cooling mechanism for motor heat, devising a new way of piping, and developing a new method of screw fastening to prevent deformation in vacuum. We also proposed operating conditions and usage methods in order to meet requests for greater thrust than anticipated. Through these and other activities, we make fine adjustments and perform maintenance. Our stance on collaboration with the customer in creating the equipment has helped us earn customer satisfaction.
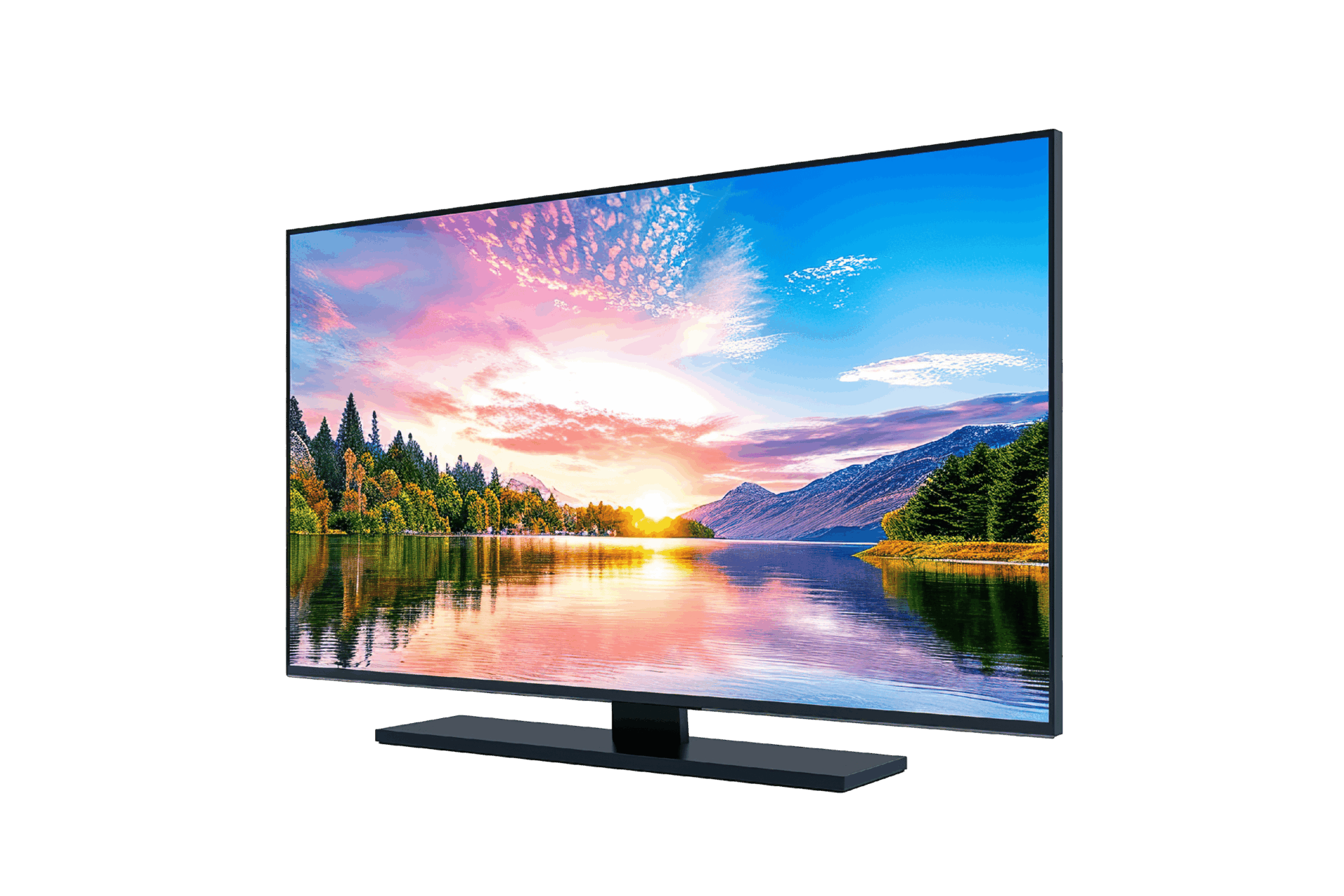
Key points in adopting our proposal
- High production efficiency of the vacuum linear servo motor
- Product quality including our know-how about vacuum linear servo motors
- Fine-tuned post-delivery follow-up system
Related products
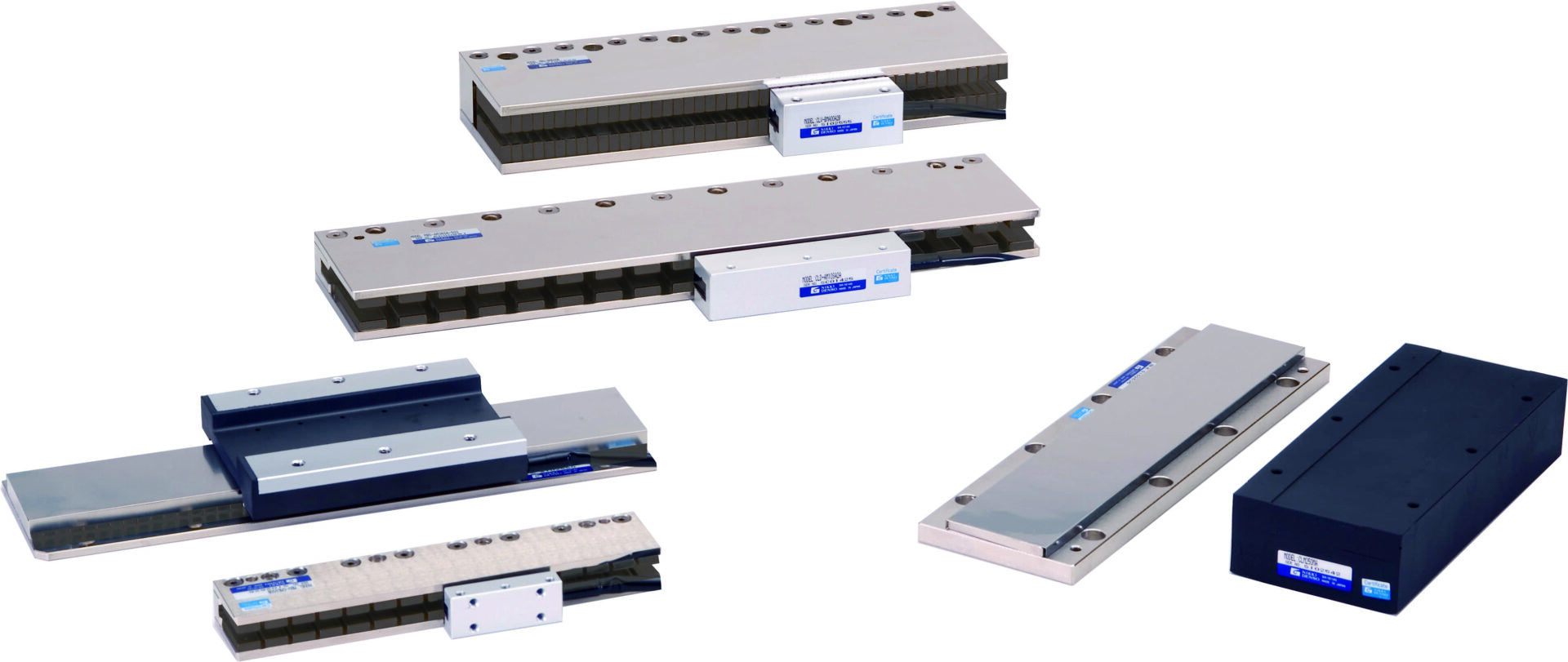
Customized product