Michishita Iron works Co., Ltd., a tufting machine manufacturer, introduced the core τLinear motors. With the rotation speed increased to about three times the previous speed, they developed a machine featuring much greater production efficiency.
The sliding needle bar (horizontal axis) in the existing mechanism has its limit, making it difficult to increase production efficiency. The customer wanted to become the industry leader by building a high-speed, high-accuracy machine.
Replacing the existing mechanism using an AC servo motor and ball screws with the core τLinear increased the rotation speed by three times to approximately 1,200 rpm, resulting in a substantial improvement in production efficiency.
[Problem] The rotation speed of the existing mechanism is limited to 400 rpm. The customer wanted to become the industry leader by further increasing efficiency.
Michishita Iron works Co., Ltd. is a manufacturer of tufting machines for carpets. The conventional tufting machine uses an AC servo motor and ball screws in its mechanical part that feeds the sliding needle bar horizontally. The rotation speed of this mechanism is limited to 400 rpm. The customer hoped to develop more efficient, high-accuracy machine.
[Proposal/solution] We calculated the torque taking into account the external forces of the slide bar in use and threads among other factors. We succeeded in meeting the required specifications by using two 1,500 N∙m linear motors.
Our calculations showed that increasing the performance of a large tufting machine having a width of four to five meters would require a force of 3,000 N∙m. So, we proposed using two 1,500 N∙m core τLinear motors in combination. This increased the rotation speed by three times from 400 rpm to 700 to 1,200 rpm, resulting in a substantial improvement in production efficiency. Michishita Iron works Co., Ltd. obtained patents for the technology of using a linear mechanism for the needle sliding device of the tufting machine in Japan, China, the U.S., and Europe. Since the motors use strong magnets, safety precautions need to be taken during production and assembly. So, we gave the customer advice on the installation method as part of our full support service.
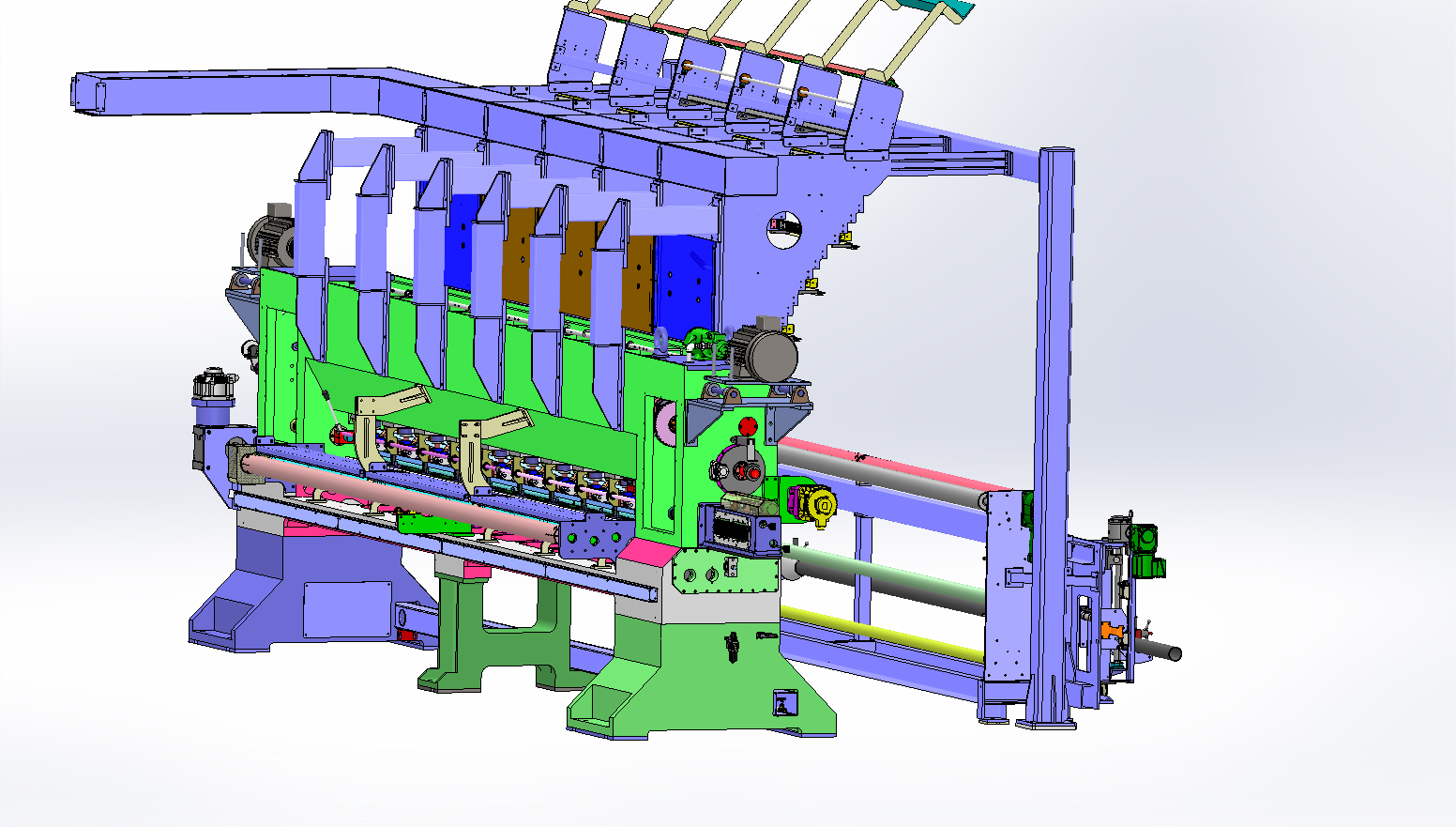
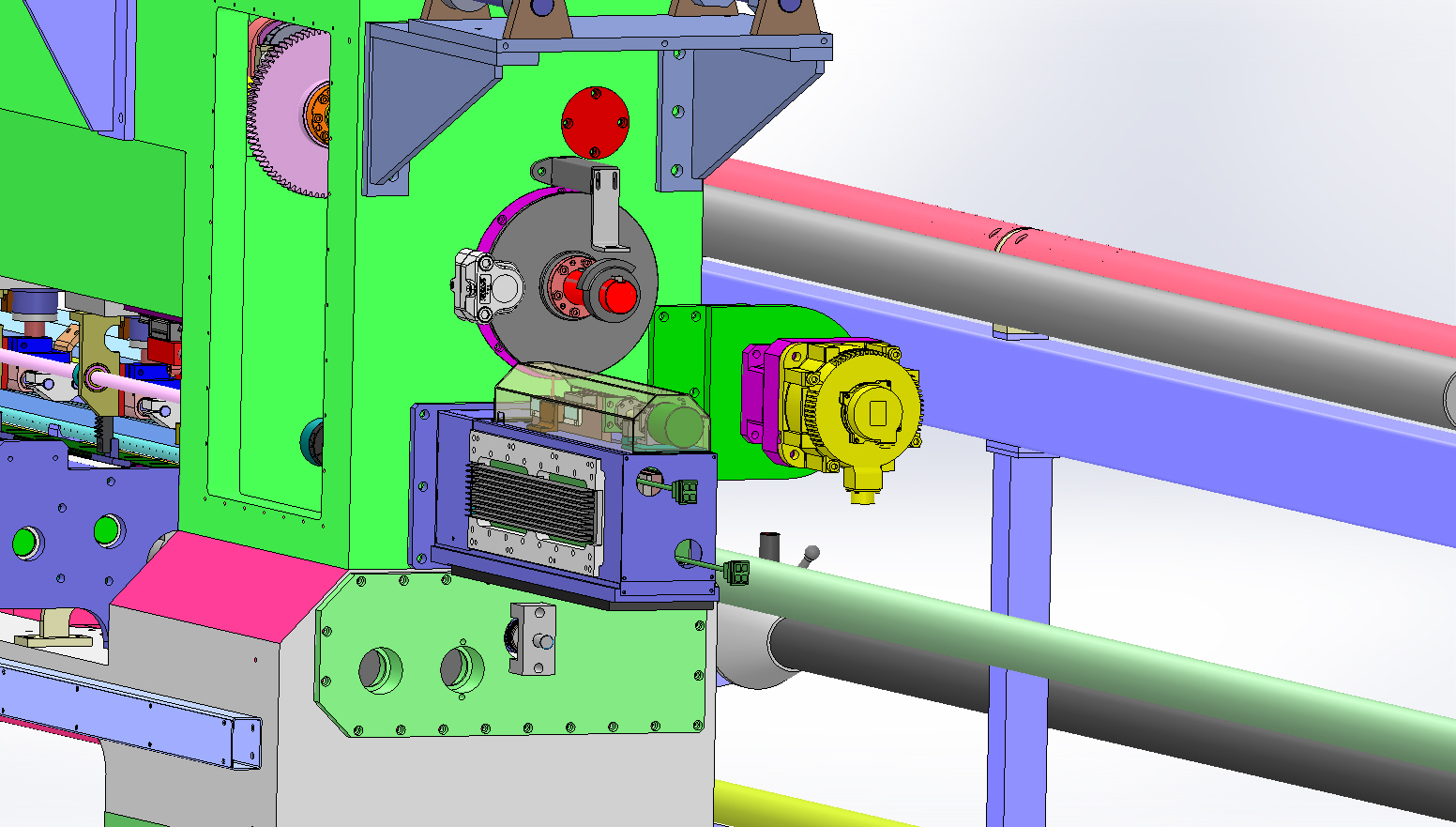
Key points in adopting our proposal
- A demo that allowed the customer to experiment with the linear servo motor with a magnet move, double sided adhesion, etc. which they had not used before
- A variety of technologies and the ability to offer proposals flexibly
- Fine-tuned support even for the introduction of the standard model
Related products
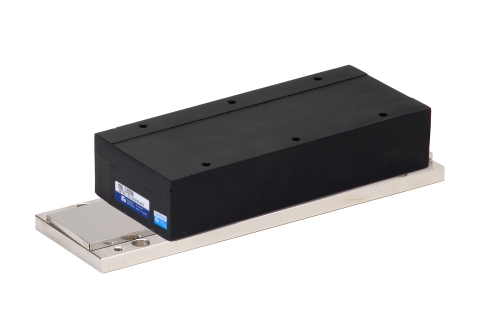
τLinear NLA-MA/NA Type