Engineer interview
At CKD NIKKI DENSO, highly skilled engineers work together, utilizing their skills, to develop servo motors and drivers – the core of the company’s business. This interview features four young and mid-career engineers engaged in the development of servo drivers, linear stages, and direct drive motors, who speak about a range of topics from their current development efforts to the future of the motor industry.
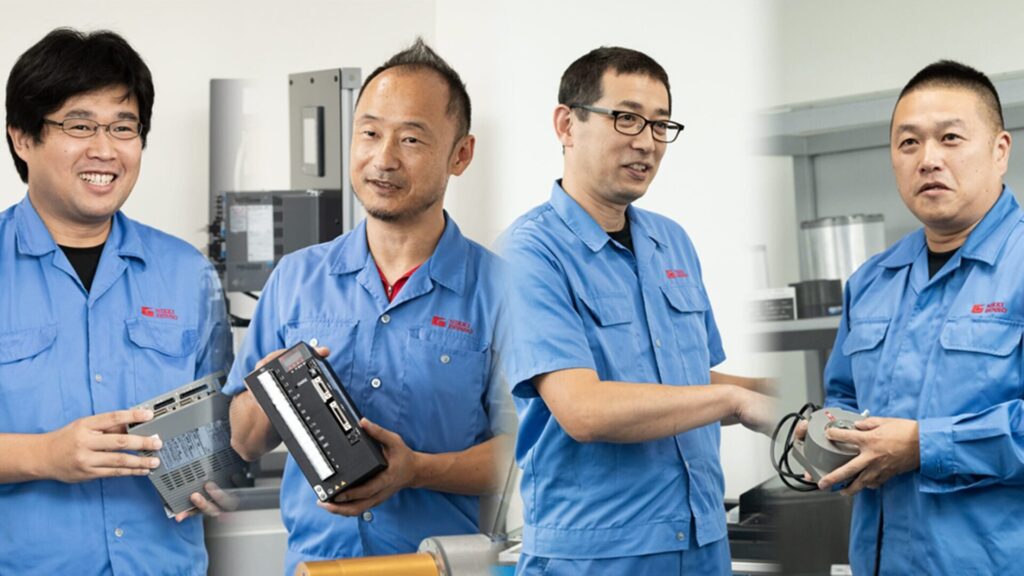
- (Left) Mr. Hagiwara, 1st Technology Section, servo drivers, power electronics design
- (Second from left) Mr. Takehara, 1st Technology Section, servo drivers, software development
- (Second from right) Mr. Ito, 4th Technology Section, linear stages, mechanical design
- (Right) Mr. Yamazaki, 3rd Technology Section, DD motors, mechanical design
Introduce yourselves briefly.
Hagiwara I design and evaluate the parts of the servo driver that are called power electronics. In addition to that, I support certification of servo drivers with regard to UL standards and CE making.
Takehara I’ve been engaged in the design of servo driver software since joining the company. I also visit customers to help them adjust and manage their machines.
Yamazaki I’m in charge of the mechanical design of DD motors and other “rotating systems.” I also design electrical parts necessary for motors, which makes my job much like motor design.
Ito I’m in charge of the mechanical design of linear stages. These are “linear systems” so to speak. The motors move linearly.
Where do you think the value of CKD NIKKI DENSO’s products lies?
Yamazaki The easiest way for us is maybe delivering standard products as they are. But I think that’s not enough for customers to find value in our products. Our motto is “consultation-based problem solving” where we solve customers’ problems through thorough discussions. We customize products to meet customer needs, and that gives added value to those products. If we only work within the boundaries of the company, it is difficult for us to get information about these needs directly from the market. I think what customers tell us gives clues about what we need to develop.
When we look abroad, overseas manufacturers create similar products, don’t they? They make products that seem to satisfy the required specifications in general. When I think about ways to gain competitive advantage against those competitors, I consider it vital how we refine our products.
Ito In the case of linear stages, sometimes the customer’s equipment has motors of different manufacturers in it. This makes it necessary to adjust the accuracy of each motor individually, and operating these motors is a cumbersome task because their user interfaces are different. Our products, by contrast, allow multiple axes to be handled simultaneously, which makes it very easy to start up the system. Even with a stage having multiple axes, like the XYθ stage, servo drivers can have a uniform interface and their accuracy can be adjusted simultaneously for the system. Customers want to put their machines into operation smoothly as quickly as possible. Many of these customers select us for our customization and support abilities that ensure that their machines work smoothly and accurately.
Hagiwara Some customers ask us to develop a servo driver for another manufacturer’s motor they currently use. There is a constant demand for such development because not so many manufacturers are able to produce servo drivers. Particularly, when customers need to use a specific motor, they often find themselves in trouble because they don’t have a servo driver that works fine for that motor.
Takehara Big manufacturers do not accommodate such small requests unless the customer purchases in quantity. These customers come to us for help at the end. For example, the factories of medical equipment manufacturers and automakers have machines that are very difficult to operate. Operating a machine like this smoothly requires thinking over details such as the current flow. So, we take the machine to our company, do experiments on both hardware and software, and bring it back to the customer for further testing. We repeat this process until the machine works in its best condition. Sometimes, we build the measures into our standard products that we have taken to solve the customers’ problems.
Hagiwara Sometimes we customize software only or hardware only, and sometimes we customize both. We customize products based on customers’ requests. Once customers introduce a customized product, they use it for as many as ten years unless it breaks down. Customers have to pay tens of millions of yen to replace equipment, so they continue to use the existing equipment until they need to upgrade it. When the existing equipment is upgraded, it is the right time for replacing our product. Some customers ask us to give them the same model they have used.
Yamazaki One big advantage we gain from customization is that we can get to see the customer’s equipment for ourselves. We look at the entire equipment along with the motor. For example, if there is some room around the peripheral devices, we could suggest making the motor a little bigger or increasing its diameter while reducing the height. If we keep addressing customers’ needs for customization, they will contact us when they upgrade their machines. If we just deliver standard products, customers will not likely see us as a development partner. I feel that catering to the customization needs of customers helps us maintain good relationships with them. Since our sales reps keep close contact with customers, like I just said, it has now become natural for customers to contact us whenever they are in trouble.
Tell us about your current development efforts.
Ito We are working with our parent company, CKD, to develop an actuator that combines our motor technology with the air bearing technology, which is one of CKD’s strengths. This is a motor that moves while floating using an air bearing. There’s the pending problem of heat, and we are now figuring out how to cool the motor. Mr. Yamazaki’s team is currently exploring ways to suppress the heat generation of the motor itself.
Yamazaki Our lineup of standard DD motors includes the high-response type HD-s Series. Slightly over 10 years after its launch, we are now revamping the motors of this series. This is because local manufacturers abroad have begun to produce similar products, threatening our brand position. It is unpractical to change all the models at once, so we are developing new models starting with the high-response motors.
Takehara The performance of the DD motor has a greater impact on the machine performance than that of the conventional AC servo motor, so the DD motor needs to move stably and fast. As a matter of fact, the speed of motor development is fast, and we have to improve the performance of the servo driver that controls the motor accordingly. So, for the servo driver we are developing, we use IT technology suitable for the new encoder. Also, the servo driver has better performance and is easier to use mechanically.
Hagiwara Speaking of ease of use, you can now operate the servo driver intuitively. For example, you can zoom in or out using the mouse wheel, instead of moving arrows around on the screen like we previously had to do.
Takehara We have a lot more analysis functions now. In the past, we had to do manual checking and visual analysis. Now, analysis is done automatically to visualize data such as how many milliseconds it takes to complete positioning and how large the torque is. The servo driver performance needs to increase in step with the advance in motors. I consider it important that we adhere to the basic principle of high performance and excellent functionality when it comes to CKD NIKKI DENSO’s products. Emerging manufacturers abroad bring many different products to market. Playing the same game with them will not set us apart. We need to keep pursuing better performance.
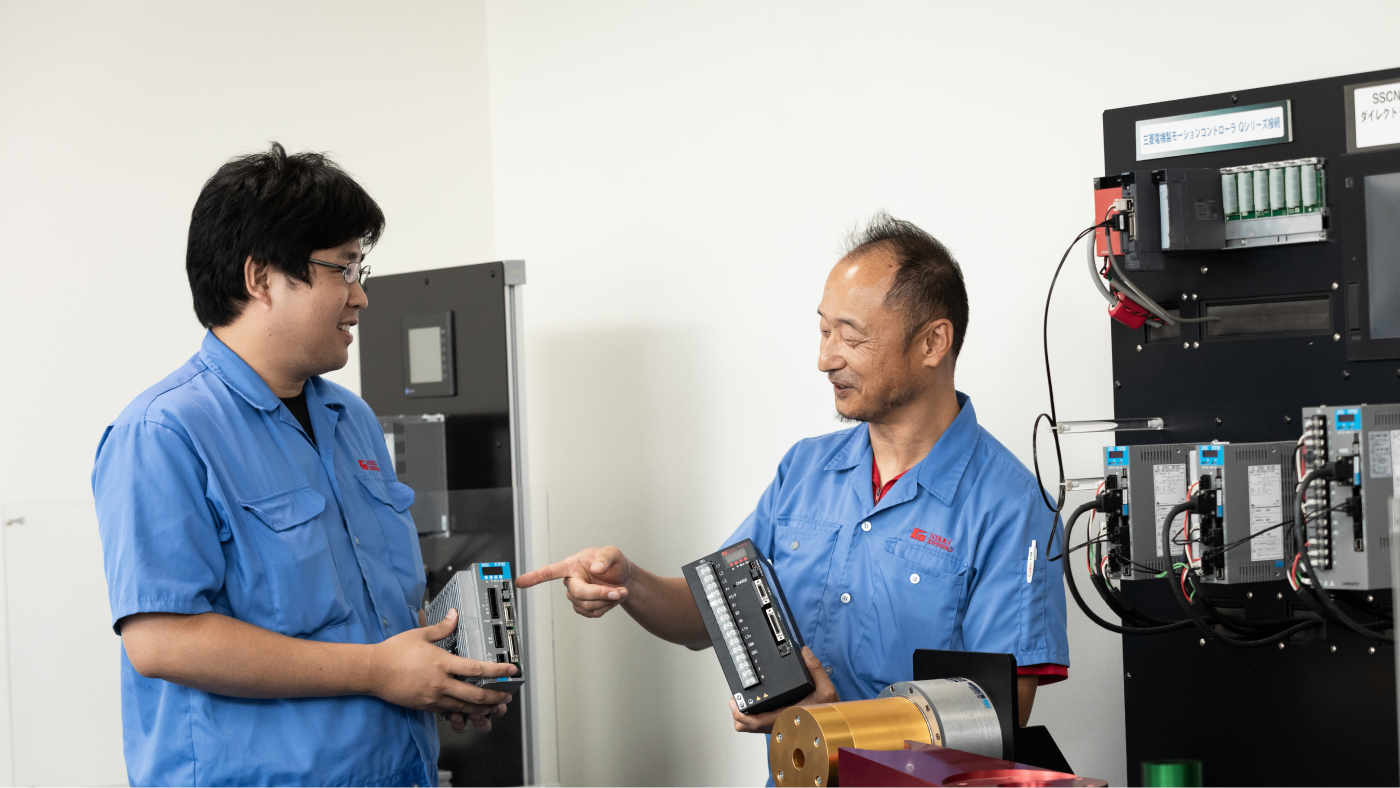
Tell us about the problems facing the motor industry at large and what needs to be done to solve those problems.
Yamazaki High response and high efficiency are major premises. That said, recent development concepts are increasingly focused on environment-conscious efforts, like curbing heat generation to prevent temperature rises and putting in place environmental regulations to reduce energy consumption. Reducing energy consumption by increasing production efficiency helps preserve the environment. I think we should address the SDGs that are inevitably required in today’s world.
Ito Similarly, the motor is required to be small in size but powerful enough to provide high output. A smaller motor makes the customer’s equipment smaller as well, which is good for the environment. But developing such a motor is very challenging. A small motor has a small heat dissipation area, which makes it difficult for the motor to cool. The dilemma is that high output requires a sufficient amount of electric power, leading to increased heat generation. We are working to solve problems like this.
Yamazaki It is also necessary to rethink about materials of the motor. If we continue to use the existing equipment, we don’t need to make any additional investment. But that doesn’t make the problem go away. Given the recent supply chain issue related to the supply of materials, not everything will necessarily go well. But I think the motor industry now faces the challenge of revamping the equipment and enhancing accuracy and material properties, even if in steps. The motor research and development efforts are directed toward savings in energy and space, and development is progressing at an increasingly faster pace. I consider it vital for us to keep up with this pace.
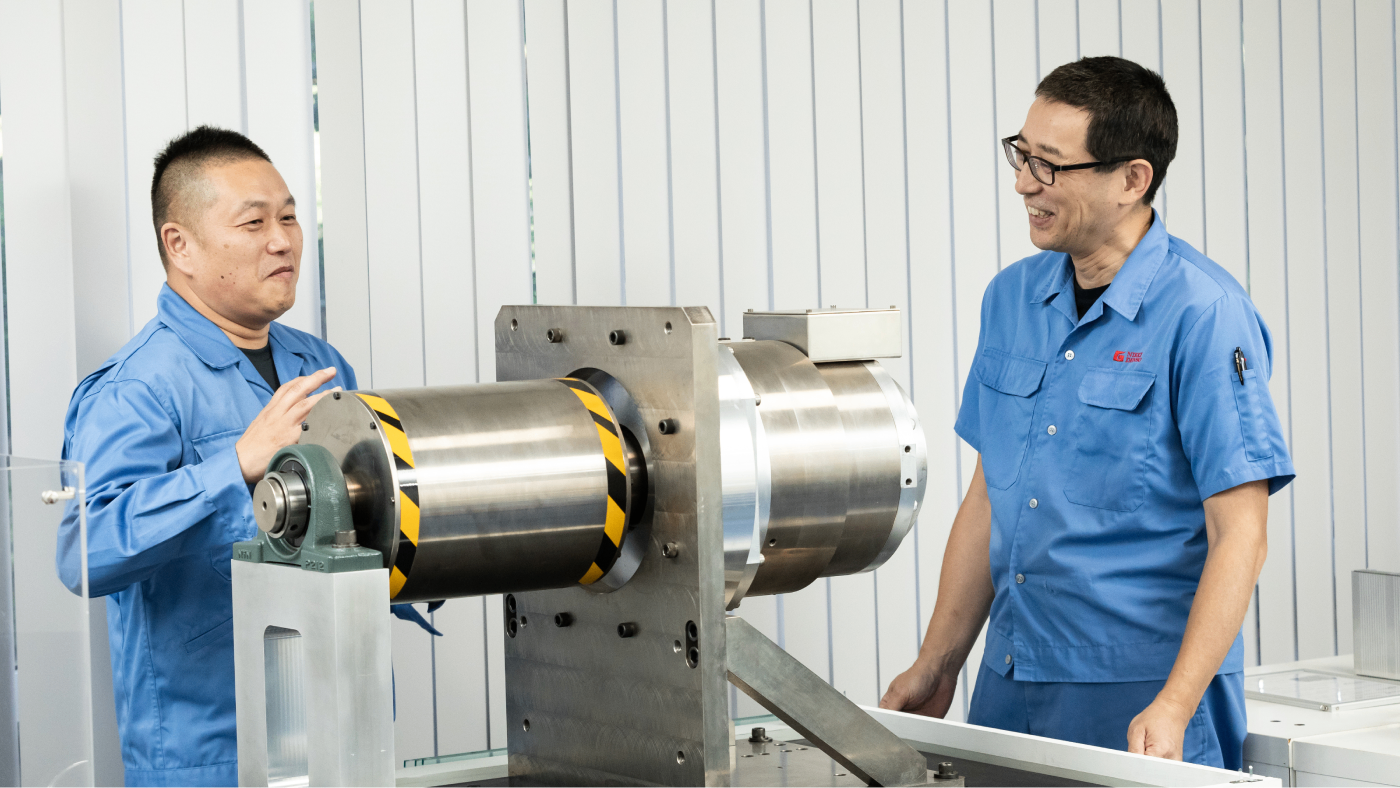
Do you have any concrete measures in mind to address the heat generation problem of motors?
Yamazaki In order to achieve low heat generation while making effective use of the characteristics of the motor magnetic circuit, we need to change the motor’s shape, magnetic material, and so on. I think this involves changing the size as well. Efforts to develop low-heat-generation motors, in my view, will continue. There is a high efficiency standard defining IE codes that categorize motors into efficiency classes, each representing a specific level of efficiency. We are going to appeal about conformance with this standard when promoting our DD motors and, hopefully, customers will pay attention to it.
Also, there’s an industry-standard size for DD motors, and products of other companies are almost the same in size, too. That’s OK when the customer introduces new equipment. But when the existing equipment is replaced with new one, it is necessary to install a motor that is exactly or about the same size as the existing motor. Our marketing research fell short of finding out if a slight difference in size would not be a problem. I think making changes including this is a way of improvement, and we are working on it step by step.
Ito Earlier, I spoke about an actuator combined with CKD’s air bearing. In addition to the problem of heat, the motor needs to use special materials because it is installed in a vacuum environment. Extra materials generate gases. Frankly, we don’t want to put extra materials, other than the copper wires of the motor, in vacuum. That way, though, the insulating performance of the motor becomes low. I consulted with Mr. Yamazaki’s team about the insulation design of the motor and other bodies. And it is now increasingly required to employ new materials that are less prone to generate gases. Since we develop both motors and encoders internally, we can start with the selection of materials of the encoder. What’s more, we have seasoned engineers who are capable of designing vacuum devices that are installed in vacuum, so we can complete all development work within our company.
There aren’t many companies that can do this, are there?
Yamazaki I think our greatest strength is our ability to respond to customer needs in a flexible, speedy manner.
Ito These days, customers increasingly demand such an ability. We need to create new products and adapt to a new environment by drastically revisit our development process. We learn new knowledge and technologies all the time to keep our consultation system trusted by customers. By implementing the cycle of “consultation-based problem solving,” we can keep learning and trying new things, which allows us to address customer needs.
Yamazaki What’s important is that we engineers should also go out in the field, rather than just work within the company. I think it’s part of our job to visit customers with our sales staff to get direct feedback from their engineers, gaining a broader range of insight and building a relationship of trust. And I think there is more beyond that, and we’ll find out about new requirements from customers.
What problems do you think there are with regard to servo drivers?
Hagiwara From the perspective of servo drivers, I presume that preventive maintenance is the problem. I mean those products that alert users before they break down. An example is a network-connected machine that automatically places orders for parts with the manufacturer before the parts reach the end of their service life. Preparations are made before failure occurs so that the customer’s machine never stops.
Takehara Actually, this is difficult unless the machine is connected to the network and the customer has a higher-level controller. AI is used for predictive and preventive maintenance. So, the current trend is that customers adopt the cloud and other services. We are now exploring ways to accomplish this with servo drivers alone. Basics and reality really matter here. You can’t use AI unless you understand the basics of design. So, engineers need to know the reality.
Hagiwara Another trend is the automation of the adjustment process. Customers have no problem as long as their machines work as they want. Automating the adjustment process makes it easier and more reliable. Going forward, we will see the adjustment process automated more and more.
Takehara In an automated adjustment process, AI does much more than humans do and provides a lot of novel findings. We are incorporating these findings one by one, and what we are debating now is where to stop. With regard to a servo driver parameter, for example, AI suggests five different answers when we previously thought there would be only one answer. We adjust the servo motor based on each of those five suggested values, and we get the same result every time. We were amazed to discover that there are so many optimal answers. When we create new servo drivers, I think we are going to build IT-based AI and analysis functions into them.
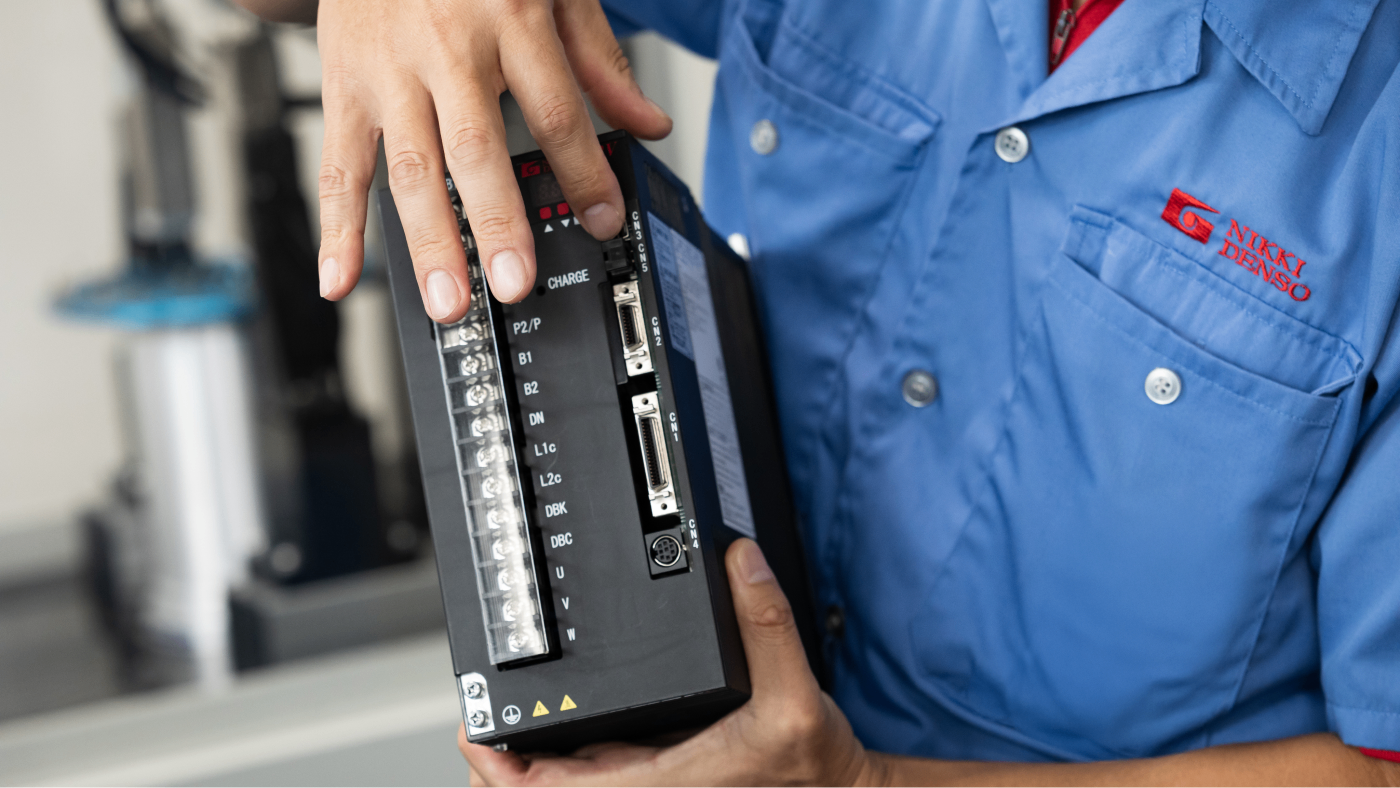
Lastly, what do you intend to do as members of the technology department in order to achieve the corporate vision and goals?
Yamazaki I consider that we are at a stage where we consider team building. When we deal with many customers with limited human resources, we inevitably end up being short-staffed. For example, there are people who can develop basic technologies and those who are capable of introducing new tools. So, we should assign the right people to the right jobs and have small groups of selected personnel introduce systems appropriate for the company and increase efficiency. Just spending a lot of time on development is not good enough. The development of new human resources is also essential. I think we need to focus on building teams like I just explained.
Ito Previous generations, including mine, accumulated experiences and developed skills by doing massive amounts of work, rather than focusing on quality. This approach of human resource development certainly helped us grow. But I don’t think it fits with the times any more.
Yamazaki I agree. There must be a way that matches the times.
Ito The company needs to choose work that helps not only the organization but also individuals grow, and they need to do so in a relatively efficient way. I think that’s the big difference from the past.
Takehara We the servo driver engineers feel the same way, too. We want to create more diverse products, but our human capital and financial resources are limited. I consider human resource development the most important thing, going forward. If you can think in a down-to-earth way, you will be able to increase your work efficiency by utilizing IT. Keep in mind, through, that when you use AI, you need people who can properly evaluate its inputs and outputs. Routine training programs are not effective in developing skills of individuals significantly. We should have the right people assigned to the right jobs, and our training should focus on the strengths of each individual member of the team. Our ultimate goal is to develop engineers who are capable of not only building a successful career in the company but also having success anywhere they go.