開発者インタビュー
CKD日機電装では事業の主軸となっているサーボモータやサーボドライバの開発において、高い技術力をもったエンジニアが、それぞれのスキルを活かし、また、お互いに協力し合いながら活躍しています。サーボドライバ、リニアステージ、ダイレクトドライブモータの開発に取り組む4名の若手&中堅のエンジニアが、今、取り組んでいる事案からモータ業界の未来までを語ります。
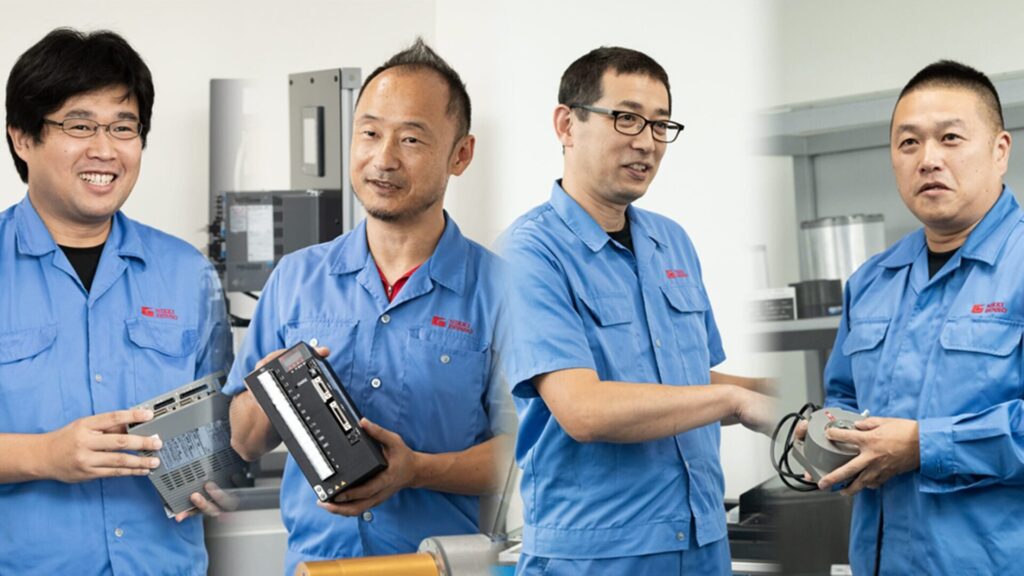
- (左)荻原氏 技術1課 サーボドライバ パワーエレクトロニクス設計
- (左から2番目)竹原氏 技術1課 サーボドライバ ソフトウェア開発
- (右から2番目)伊藤氏 技術4課 リニアステージ 機械設計
- (右)山崎氏 技術3課 DDモータ 機械設計
簡単に自己紹介をお願いします
荻原 サーボドライバの中のパワーエレクトロニクスと言われる部分の設計と評価を担当しています。それ以外にもサーボドライバのUL規格やCEマーキングといった認証の対応もしています。
竹原 サーボドライバのソフトウェア設計を入社以来、担当しています。また、お客様のところに伺って機械の調整サポートや管理もしています。
山崎 DDモータなど“回転系”の機械設計を担当しています。機械設計以外にモータに必要な電気的な部分も一緒に担当しているので、モータ設計に一番近い仕事になりますね。
伊藤 リニアステージの機械設計を担当しています。いわゆる“直線系”ですね。直線に動くモータです。
CKD日機電装の製品の価値は、どんなところにあると考えていますか?
山崎 本当は標準品をそのまま納品するのが一番楽なのかもしれませんが、それだけでは当社の製品の価値を見出すのは難しいと思っています。当社のモットーは、お客様としっかり向き合って悩みを解決していく「相談解決」です。当社が売りたい製品ではなく、お客様のニーズに対応できるよう製品のカスタム対応を行うことで製品に付加価値が生まれます。市場要求は社内にいるだけではなかなかダイレクトに入ってこないもので、お客様から伺った話の中に開発のヒントがあると考えています。
世界を見れば、海外のメーカーも当然同じようなものを作ってくるじゃないですか?見かけの仕様に合わせ込んでくるので、そこに対してどう優位性を出すかを考えた時、当社の製品をどういうふうに作り込むかが直結してくるのではないかと思うのです。
伊藤 リニアステージでXYθステージなど複数軸の場合、お客様で複数のメーカーのモータを組み合わせて製作するとそれぞれ精度の調整が必要になったり、ユーザーインターフェースが異なるので手間がかかるんです。当社では、XYθステージなど複数軸をまとめて精度調整したシステムで対応でき、サーボドライバのインターフェースも統一できるので非常に立ち上げやすいと思いますね。お客様としては早くスムーズに機械全体を動かしたいので、滑らかに正確に動かせるカスタム対応とサポート力をかわれて採用されることが多いですね。
荻原 お客様から、今使っている他社製モータに合わせたサーボドライバを開発して欲しいというご要望もありますね。サーボドライバを作れるところはあまり無いので、そういう要求は一定数あるんです。特にモータありきみたいな状態だとそのモータを使いこなせるサーボドライバが無くて困っているお客様もいらっしゃいます。
竹原 導入数が少ないと大手のメーカーさんはそんな細かいところまでやってくれないので、最終的に当社に相談しにこられますね。例えば医療機器メーカーや自動車メーカーの工場で、回して動かすだけでも難しい機械があるのですが、そこをうまく回すためには電流をどういうふうに流すのかなど再考しなければいけないので、何回も持ち帰って、ハードとソフトの両方で実験して、またお客様のところへ持っていってテストして……最適なところまで持っていくっていう感じ。そういうお客様のところで実際にあった困りごとへの対策を自社の標準品に組み込むこともあります。
荻原 ソフトウェアだけのカスタムやハードウェアだけのカスタム、もしくは両方とか。そもそもカスタム製品はお客様の要求をもとに作っているので、ひとつ導入されたら壊れない限り10年くらいずっと使ってくれていますね。お客様の設備は取り替えたら何千万円とかかかりますから、設備自体をリニューアルしない限りは使い続けますよね。ですのでリニューアル時がこちらの製品も取り替えるタイミングになるのですが、中には今までと同じ機種を持ってきてほしいというお客様もいらっしゃいますね。
山崎 実際、カスタム対応のメリットは、お客様の装置も見させていただいてるっていうところも大きいですね。モータと一緒に機械自体を見ているので、例えば周辺装置にもう少し余裕あれば、もうちょっとモータを大きくしても大丈夫じゃないかとか、径を大きくして高さを短くしてもいいんじゃないかとか、そういうことをお客様にも提案できるんです。しっかりとカスタム対応を続けていれば、お客様の方でも機械のリニューアルをするときに、また私たちにご相談をいただける。標準品を納品しているだけだと、「一緒に開発を行う」という関係性にはなりにくいため、お客様に寄り添いカスタム対応を行っていくことでお客様と良い関係が保てるのではないかと感じます。そういった形で営業がお客様に密着しているので「困ったらCKD日機電装に相談しよう」という流れができてるのだと思いますね。
新しく取り組んでいる開発内容について教えてください
伊藤 今、親会社のCKDと一緒に、CKDの強みとなっている流体軸受エアベアリングと、当社のモータの技術と掛け合わせたアクチュエータの開発をしています。エアベアリングで浮きながら動くモータなのですが、どうしても発熱の問題がありまして、それをどうやって冷却するかを考えています。発熱自体を少なくするのは山崎さんのチームで、モータ自体の発熱を抑える方法を考えてもらっています。
山崎 DDモータの標準ラインアップとして高応答タイプのHD-sシリーズというものがあるんですけど、発売から10年ちょっと経っているためリニューアルを進めています。海外のローカルメーカーが同じような製品を作るようになって、当社のブランドポジションが侵されつつあるためです。なかなか全てのモデルをリニューアルするわけにはいかないので、まずは高応答のモータを皮切りにリニューアル開発を進めています。
竹原 DDモータの場合、モータの性能が従来のACサーボモータよりもかなり高い比率で機械の性能に影響してくるため、安定して速く動かすことが求められます。実際、モータの開発スピードが速く、それを制御するサーボドライバも性能を上げていかないといけないので、開発中のサーボドライバには新型のエンコーダに適合するIT技術を投入して開発しています。あとは性能アップと機能的に結構使い勝手が良くなっていると思います。
荻原 使い勝手の例で言うと、今まで画面の中で矢印をカチカチ動かしていたのを、マウスホイールで拡大縮小するなど、感覚的に動かせるようになっています。
竹原 解析できる機能はかなり増やしてます。今まで手動で調べて人の目で見て解析していたのを、位置決め時間が何msecでどのくらいトルクを使っているかなども自動で解析して見える化できるようになっています。モータの進化とともにサーボドライバも一緒に性能を上げる必要があります。やはりCKD日機電装の製品は高性能・高機能というところはブレてはいけない基本路線だと思います。海外の新興メーカーなどもいろんなものを出してきたりするんですけど、そことまともにやりあってもうちの特長は出ないので、常に性能を追い求めていく必要がありますね。
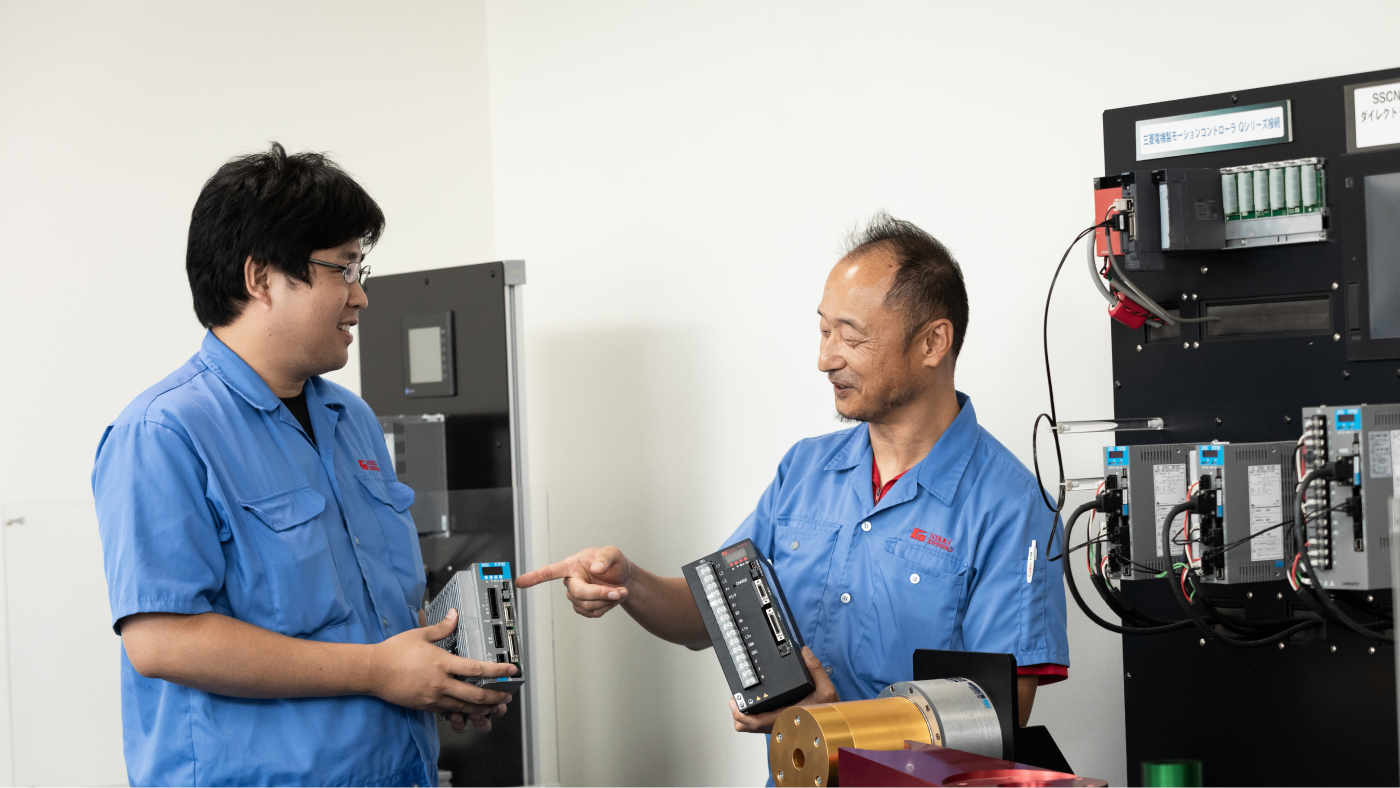
今のモータ業界全体の課題と、課題解決するためにはどのような取り組みが必要か教えてください
山崎 例えば高応答と高効率は大前提なのですが、発熱して温度が上がってしまうのを改善しようとか、環境保護的な規制などでエネルギーを抑えようなどといったことが、最近の開発コンセプトの主軸になっていますね。生産効率を上げることによってエネルギーの消費を抑えられれば、環境への配慮につながります。今まさに時代に即したSDGsに、少しずつでも取り組んでいくべきだと思っています。
伊藤 同じようにモータは小さいけれど出力が高く力強いモータが求められていて、そうするとお客様の装置自体が小さくなるので、そういう意味では環境に良いモータなのですが、逆に開発が大変で苦労してまして。小さいと放熱面積も小さいから冷えないんですよね。かつ力を出すために電力はそれなりに必要なので発熱は高くなるというジレンマ。そういう課題を解決しようとしてるところです。
山崎 モータの材料の見直しも必要ですよね。今まで使ってきたものを資産として使っていけば、設備投資をせずに済むとは思うんですけど、もうそれではごまかしのきかないところまできていると思います。最近はサプライチェーンの材料供給問題もあるので一概に全てうまくいくとは限らないですけど、例えば設備を見直して、今より一段階でも精度を上げるとか、材料特性を上げていく時期がモータ業界全体としても課題になっていると思います。モータの研究開発の方向性としても、省エネルギー省スペースという方向になり、ますます開発スピードのサイクルが早くなってきてるので、乗り遅れないようにすることも課題としてはあるんじゃないかな。
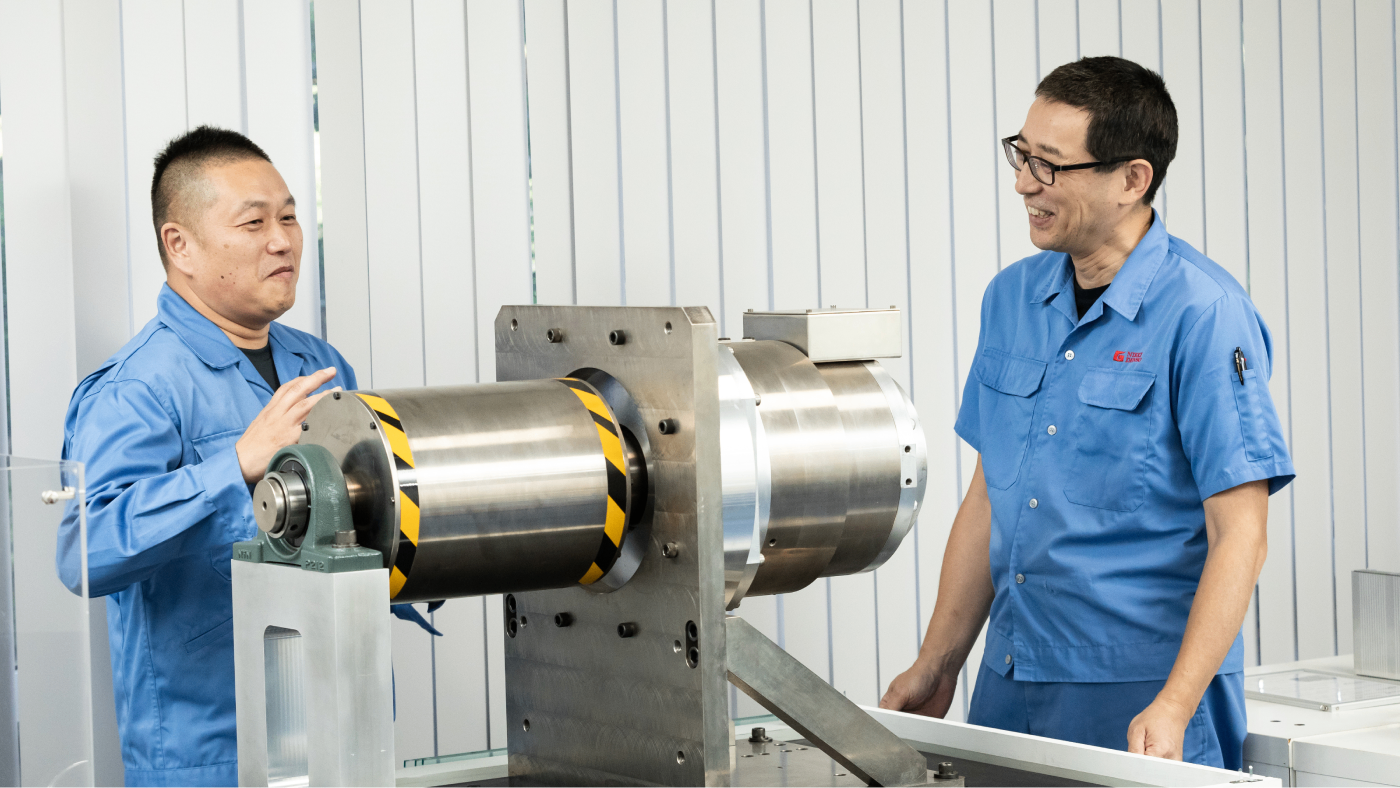
モータの発熱に対して具体的にどのような対策を考えていますか?
山崎 モータの磁気回路の特性をより効率的に発揮しつつ、さらに低発熱を追求するには、形状や磁性材などの見直しをする必要があります。そのためにはサイズも見直すべきなのではないかと考えています。発熱の低いモータの開発はこれから続くんじゃないかなと思います。モータには高効率の効率クラスをIEコードで識別された高効率規格というものがあり、DDモータもこれからそういう規格をうたっていくことで、お客様もそこを見てくれると思います。
また、DDモータには業界標準サイズのようなものがあるので、他社さんも同じぐらいのサイズになっています。機械が新規だったらいいのですが、置き換えだと同じ、あるいは近いサイズを取り付けることになります。でも、少しサイズが違っても問題ないかどうかマーケティングできてないところもあったので、そこも含めて見直しをかけていくのも一つの手だと考えていて、少しずつ取り組み始めています。
伊藤 先ほどお話ししたCKDのエアベアリングと組み合わせたアクチュエータですが、発熱の問題の他に、真空の環境下に置くものなのでモータに使う材料が特殊なものになります。余計な材料が入っているとそこからガスが発生するので、極端にいえばモータ銅線以外の余計な材料は真空下に入れたくないんです。でもそのままだとモータの絶縁性能が低いので他のボディーとモータの絶縁設計をどうしようかと。山崎さんのチームにも相談してガスが出にくい材料を新しく採用するなど、そういう流れが新しく要求されています。モータとエンコーダの開発も自社で全部やっているので、エンコーダも素材から。さらに真空に収める真空機械設計ができるベテランのエンジニアがいますので、社内ですべての開発が完結します。
そんなことができる会社って他にあまりないですよね
山崎 融通が利くというか、スピード感も含めて対応できるのが一番の強みかと思いますね。
伊藤 最近、お客様側のニーズもそこが多くなっています。開発を根本的に見直していくことで、新しいものが生まれて新しい環境に対応していかなきゃいけない。お客様から信頼され相談してもらえる体制をずっと続けていく、という形を続けるために、我々の方も新しい知識や技術を常に勉強しています。「相談解決」のサイクルを回すと、常に新しいことを学んでチャレンジしていけるので、お客様からのニーズにも応えられるということです。
山崎 大事なのは我々エンジニアも社内にとどまらずにフィールドに出ていくことですね。生の声を聞きに営業と一緒にお客様の技術担当者と直接話すことで、知見を広めながら信頼関係を築くことを僕らがやらなければいけないのかなと思います。そこにその先があると思いますし、求められる要求も生まれてくるのかなと思ってます。
サーボドライバではどんな課題があると感じていますか?
荻原 サーボドライバの立場から見た課題は、予防保全でしょうか。要は壊れる前に警告を出す製品です。例えば、部品の寿命が来る前にネットワークにつないでいれば自動的にメーカーの方にも部品の発注がされるとか。壊れる前にあらかじめ準備してお客様の機械が止まらないようにする。
竹原 それは基本的にはネットワークにつながっていて上位コントローラーを持ってないと難しいところはあるんですけど。予知・予防保全はAIを使うので基本的にはクラウドなどを持ちつつやるというのが今の流れですね。それをサーボドライバだけでやれる方法を考えています。基本とリアルが大変重要になってくるので、設計の基本をわかってないとAIも使えないから、とにかくエンジニアは現実を知らないといけない。
荻原 あと調整の自動化ですね。お客様としては思った通りに動けばいいし、それを自動でやってくれた方が楽だし確かなので、これからは調整の自動化がどんどん進んでいくと思います。
竹原 自動化すると人間ではやりきれないぐらいのことをAIがやれてしまうので新しい発見は多いです。徐々に取り入れて、どこで見切りをつけようかなっていうのが今一番迷っているところですが。例えば、サーボドライバのパラメータの結果に対して、今まで1個の結果しかないだろうと思ったのがAIだと例えば5通りとかの答えが出てくるんですよね。その5通りの調整をしても同じ結果になるという、最適の答えがこんなにたくさんあるということは新しい発見でした。新しいサーボドライバを作るときにも、ITの技術を使用したAIや解析機能を組み込んでいこうと考えています。
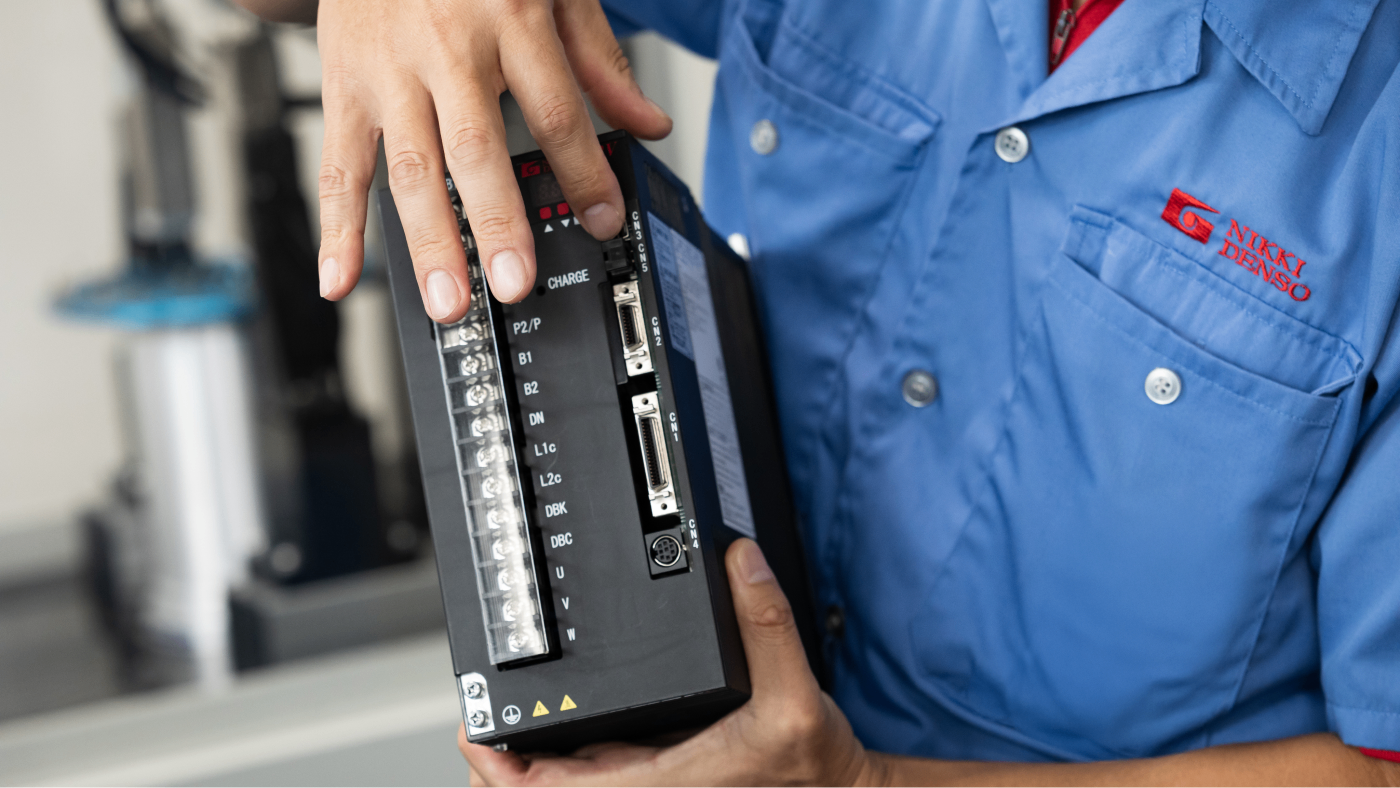
最後に、会社全体のビジョンや目標を達成するために、技術部門としてはどういうことに取り組んでいきたいとお考えでしょうか?
山崎 組織の作り方を考える段階だと思っています。限られたメンバーでさまざまなお客様の対応をしているとどうしても工数が足りなくなっていくので、例えば要素開発に選任できる者、新しいツールを導入できる者など担当を割り振って、少数精鋭で自社に合ったシステムを導入して効率を上げていくべきかと。開発自体も手間だけかければいいわけではないし、新しい人材育成も必要です。そういったチーム作りをしていきたいですね。
伊藤 私たちの世代までは人材育成については質というより量をこなして経験積んで成長してきた世代だったので、それはそれで成長してきたのですけど、これからはそういう時代じゃないと思うんですよね。
山崎 そう、時代にマッチしたやり方っていうのがあるはずです。
伊藤 会社としては個々も成長できる案件を比較的効率よく選んでいかないといけない。それが昔と全然違うと感じています。
竹原 私たちサーボドライバの側も全く同感で、もっといろいろなものを作りたいですけど人的資本や資金が限られているから、これからは人材育成が一番大事だと感じています。地に足がついた考え方をできるようになっていれば、あとはITの力を使えば効率化はできるんですよ。ただ、AIなどを使うにはどういうインプットを使ってどういうアウトプットが出てくるかをきちんと評価できる人が必要になってきます。一律的な教育では個人の力を大きく伸ばせないので、適材適所、メンバーそれぞれの強みを活かした教育を心掛けていきます。社内だけでなく結果的に世の中どこに行っても通用する技術者を育成したいですね!